E-Archive
Interview
in Vol. 17 - September Issue - Year 2016
Go and See - Practical Relevance is the Lifeblood of Successful Project Management
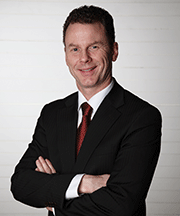
Thomas Gstettenbauer, Vice President of Project Management at D
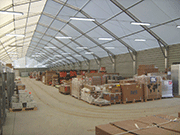
Storage on site
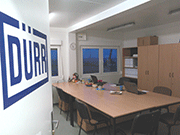
Campus on site
The Dürr Group is one of the world's leading mechanical and plant engineering firms. Products, systems and services offered by Dürr enable highly efficient manufacturing processes in different industries. Business with automobile manufacturers and their suppliers accounts for approximately 60% of Dürr's sales. Other market segments include, for example, the mechanical engineering, chemical and pharmaceutical industries and - since the takeover of HOMAG Group AG in October 2014 - the woodworking industry. Dürr has 92 business locations in 28 countries. With just under 15,000 employees, the Group generated sales revenues of € 3.77 billion in 2015. The Dürr Group operates in the market with five divisions: • Paint and Final Assembly Systems: paint shops and final assembly systems for the automotive industry • Application Technology: robot technologies for the automatic application of paint as well as sealants and adhesives • Measuring and Process Systems: balancing and cleaning systems as well as assembly, testing and filling technology • Clean Technology Systems: exhaust-air purification systems and energy-efficiency technology • Woodworking Machinery and Systems: machinery and systems for the woodworking industry
7,500 tons of installed steel, up to 1,450 technicians working side by side at the construction site and a contract volume to match: Erecting the paint shop for the new Volkswagen plant in Wrzesnia, Poland is one of the largest orders Dürr has ever received. Shortly before the facility is commissioned, everything runs exactly to plan. Vice President Thomas Gstettenbauer, who oversees project management activities for the plant engineering firm, reports in an interview how global projects are carried out at Dürr.
(?) MFN: Mr. Gstettenbauer, you and more than 100 employees in the project and construction site management team are currently coordinating 25 large-scale projects in the painting and final assembly areas. What is your biggest challenge?
(!) T. G.: The new paint shop for Volkswagen in Poland, for which we are providing all handling and processing equipment for the new Crafter - a transport van that measures up to 7.3 meters in length and has 85 m² of surface area to paint - is quite a big challenge indeed. In the steel construction alone, we have mounted some 5 football fields of platforms and installed 640 meters of drying equipment, 1,000 meters of work stations and 7.6 km of conveyor systems, not to mention routed 650 km of cable. The fact that we have also been commissioned to erect the building as a general contractor makes the endeavor even more demanding. Regardless of the volume, however, the factors that determine the success of every project have always been the delivery scope, time, quality and costs. For our customers in the automotive industry, the most important criterion is the start of production, or SOP. If this deadline is overshot, heavy contractual penalties can be imposed. Thankfully, Dürr is known for meeting project deadlines.
(?) MFN: How do you manage to carry out projects just in time?
(!) T. G.: Over the last few years, we have continually worked on optimizing our processes as they lay the foundation for ensuring that projects are completed smoothly and efficiently. Our primary goal is to implement every step correctly at the first go as this allows us to stay on schedule while minimizing follow-up costs. And we achieve this by documenting in great detail all the changes and problems that arise during a project, which we then incorporate into a lessons learned file. In this file, we jointly define which measures must be implemented to ensure that the same mistake is not made in the next project.
(?) MFN: What skills help you prevent complex, large-scale projects from becoming derailed?
(!) T. G.: We have been planning and implementing overall systems for painting and final assembly for over 50 years. With a total annual project volume of 1 billion euros, we have a very sizable market share and cater to our customers worldwide with 33 company-owned subsidiaries in 22 countries. Regardless of where a customer wants to set up a paint shop, our global collaboration with competence centers and local national subsidiaries means that we are very familiar with country-specific conditions such as legal regulations, cultural customs and climatic requirements.
(?) MFN: Constraints and process environments are very different around the world. How does this impact quality?
(!) T. G.: For us, there is no difference between a paint shop in Germany and one in another country as both are realized to perfection from a technical perspective. This is what makes the "Made in Germany" label so respected worldwide. China is a good example that proves we implement nothing less than highest quality standards. By carrying out a large number of projects there, our staff of more than 2,000 employees in Shanghai quickly aligned themselves with our way of doing things, and we are very proud of the work they have done.
(?) MFN: Can you elaborate on how things are coordinated at the construction site in such a way that unified standards are met worldwide?
(!) T. G.: A milestone was our new "Campus on Site" concept, which brings together all Dürr units under one roof and employs open structures to offer ideal working conditions that facilitate communication in a project. As a general contractor, we also define the procedures that our suppliers and subcontractors must also follow. The installation phase for the assembly teams, for example, always starts with a kick-off workshop on project execution, quality standards, safety and cleanliness on site. Before an element such as a pipe can be fitted, we weld a sample to evaluate and specify the standard. Another important factor is that our site supervisors check to see if everything is going according to plan in line with our "go and see" practice.
(?) MFN: What does this practice entail?
(!) T. G.: "Go and see" reflects the many years of experience I have gained working as a project manager. I cannot improve anything if I only sit at my desk. I need to physically see what is going on outside. Even in my current position, I am only rarely in my office in Bietigheim-Bissingen for four weeks in a row. Despite modern media, I still hold one-on-one contact as being indispensable, and when visiting employees on site, I take the time to express my appreciation for the work they do, as this is a real motivator.
(?) MFN: Project management comprises many building blocks. Which of them do you focus on?
(!) T. G.: We strive to carry out projects reliably and promote open communication. Our teams around the world work according to standardized processes utilizing state-of-the-art technology that provides quick and effective access to all relevant information and data. Throughout the course of the project, we create status reports on a weekly basis that include target-actual comparisons for each individual area, among other key indicators. This, in turn, allows us to respond quickly to problems so that we can reach all milestones leading up to the SOP while keeping our clients well informed of our progress. We also generate monthly reports that summarize all deadlines, financial and organizational details. One of the unique aspects of our project management style is that we engage in a team engineering session with our customers as soon as a project is started. In this meeting, we agree on the scope of the project based on the tender and initial drawings and layouts so that we avoid any misunderstandings later on.
(?) MFN: One more personal question: What qualities do you need as a project management coordinator?
(!) T. G.: Strong nerves, a pronounced ability to organize things, and the capacity to think strategically. It is not enough to simply keep things going at an operative level as you need to know in what direction your area must develop and which processes can be further optimized. An interdisciplinary function I pursue helps me out in this regard; for twelve years, I have run the Center of Excellence for Project Management, which integrates all processes, tools and training seminars on project management throughout the entire Dürr Group. Since 2011, we have trained over 400 employees and continue to advance and further project management activities at Dürr.
MFN would like to thank Thomas Gstettenbauer for this interview!
For Information:
Dürr Systems GmbH
Günter Buzer
Marketing - Paint and Final Assembly Systems
Carl-Benz-Str. 34
74321 Bietigheim-Bissingen, Germany
Tel. +49.7142.78-2614
E-mail: guenter.buzer@durr.com
www.durr.com
